[:pb]Já falamos aqui sobre O que é a Indústria 4.0, e a Indústria 4.0 na prática. No post Indústria 4.0 na prática mostramos um exemplo realista de como a Indústria 4.0 faz uma enorme diferença nas perdas por quebra/manutenção de máquinas. No caso utópico citado no post, uma das tecnologias usadas é a Manutenção Preditiva. Mas será mesmo que ela é tão utópica assim?
Confira abaixo!
O que é Manutenção Preditiva?
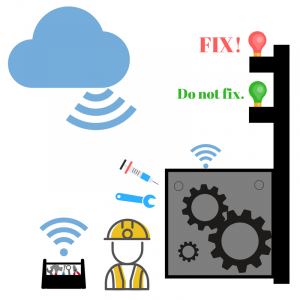
É horrível quando você está no seu carro e ele quebra, não? Mesmo com todas aquelas revisões caras, ele acaba deixando você na mão, e quase sempre em momentos em que você não pode se atrasar para o compromisso ao qual estava a caminho. Agora, imagine que o seu carro fosse “inteligente” o suficiente para perceber quando algum de seus componentes está próximo de quebrar. E se ele pudesse te avisar para visitar o mecânico, e ainda indicar a ele qual peça necessita de reparo?
Na fábrica, situações parecidas acontecem, máquinas quebram no final do mês, atrasando a produção quando a linha já está sobrecarregada, correndo atrás da meta. E pior, o tempo gasto na investigação e solução do problema faz com que outras máquinas que dependem da que quebrou também parem. E neste caso, se a máquina fosse “inteligente” o suficiente para perceber que está perto de quebrar, e pudesse avisar o responsável pela manutenção que ela precisa de serviço na peça X?
Estas “inteligências” citadas em ambos os exemplos são o que chamamos de Manutenção Preditiva.
Entendendo os tipos de manutenção
Existem três tipos de manutenção, são elas:
- Manutenção Corretiva: Quando o equipamento tem alguma pane, e precisa de reparos para voltar a funcionar. Normalmente toma muito tempo, pois o equipamento fica inutilizável enquanto os especialistas investigam a causa do problema. Além disto, por ser inesperada, pode causar muitos problemas na cadeia de produção.
- Manutenção Preventiva: É feita utilizando algum parâmetro externo a máquina para determinar quando deverá acontecer. Por exemplo, é feita a cada 480 horas de equipamento operando, ou a cada 10000 km rodados pelo automóvel. Não necessariamente garantem que o equipamento não irá falhar, mas reduzem muito essa possibilidade. Como o intervalo entre manutenções é pre-determinado, elas podem não refletir todo o contexto em que o equipamento está inserido. Por consequência, pode levar a gastos com manutenção desnecessária, desperdício de partes que ainda estavam boas para operar, etc.
- Manutenção Preditiva: O equipamento se monitora, sabendo a todo tempo o estado de seus componentes. Com isto ele também prevê quando há uma falha iminente, avisando que precisa de manutenção e dando informações que ajudam o técnico a saber qual parte do equipamento precisa de manutenção. Com o uso da Manutenção Preditiva é reduzido o risco de falha e também o desperdício de tempo e material com manutenção preventiva.
Como é possível aplicar Manutenção Preditiva?
Como explicado no post IoT and predictive maintenance, do Bosch ConnectedWorld Blog, a Manutenção Preditiva é viabilizada a partir de três passos:
- Captura de dados de sensores: Colocar diversos sensores no recurso a ser monitorado. Diversas grandezas no equipamento devem ser medidas com frequência, e disponibilizadas para processamento. Devido ao grande volume de dados adquiridos, esses dados poder ser considerados Big Data. Na maior parte do tempo, a medição seguirá um padrão, porém um desvio deste padrão pode indicar um evento.
- Facilitar comunicação de dados: Os dados coletados no recurso devem ser transferidos para uma central de processamento de dados. Para um bom tempo de resposta a mudanças no padrão de medição dos sensores, é ideal que a transferência dos dados para a central não demore.
- Fazer predições (IA): Os dados dos sensores são avaliados constantemente, e comparados com padrões históricos. Quando um padrão similar aquele que costuma acontecer antes de um evento (uma quebra, por exemplo), o sistema reporta o comportamento. Com isso, ações devem ser tomadas pelo sistema para reverter o evento, como por exemplo, avisar o responsável pela manutenção que o recurso X tende a apresentar o defeito Y na peça Z nas próximas horas.
Como entender tantos dados?
Nenhum dos três passos descritos é tarefa fácil, mas o mais desafiador é o terceiro: fazer predições.
Para tal, inicia-se pela seleção e pré-processamento dos dados a serem processados (Data Mining). No algoritmo de Data Mining, os especialistas no recurso e cientistas de dados podem representar explicitamente conhecimentos adquiridos pela experiência. O algoritmo irá expandir este conhecimento, encontrando relações entre as variáveis disponíveis.
Após o pré-processamento, vem a parte de análise de comportamento e padrões. Esta parte é feita com algoritmos de Inteligência Artificial, que são capazes de aprender como são os padrões que geram cada evento. Eles são utilizados para monitoramento e detecção destes eventos.
Detectado o evento, o programa verifica se é necessário uma ação, e dá início a ela. Esta ação pode ser desde um controle na máquina até o envio de mensagens ao pessoal responsável.
Como começar?
Implementar a Manutenção Preditiva em uma fábrica inteira certamente não é tarefa fácil (ou barata), mas vimos que os benefícios são muitos. Um projeto ambicioso deste tamanho requer pequenos passos para sua implementação com sucesso.Sugerimos que comece avaliando quais ferramentas usadas na Manutenção Preditiva sua fábrica já possui e liste os equipamentos com maior nível de conectividade e maior quantidade de sensores disponíveis.
Você já centraliza os dados coletados por estes equipamentos? Verifique também se o fabricante coleta, armazena e disponibiliza dados sobre seus equipamentos. Estes dados podem ser usados para comparação e treinamento de um algoritmo de Inteligência Artificial.
E sua fábrica, possui sistemas que podem ser utilizados/adaptados para implantação da Manutenção Preditiva? Conte-nos nos comentários.
Lembre-se que podemos ajudá-lo nestes projetos para sua fábrica, basta entrar em contato com a gente.[:es]Ya hablamos aquí sobre qué es la industria 4.0, y la industria 4.0 en la práctica. En el post industria 4.0 en la práctica mostramos un ejemplo realista de cómo la industria 4.0 hace una enorme diferencia en las pérdidas por rotura / mantenimiento de máquinas. En el caso utópico citado en el post, una de las tecnologías usadas es el Mantenimiento Predictivo. Pero será que ella es tan utópica así?
Echa un vistazo!
¿Qué es Mantenimiento Predictivo?
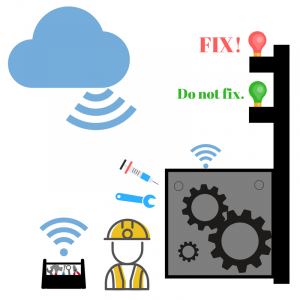
Es horrible cuando estás en tu coche y él se rompe, ¿no? Incluso con todas esas revisiones caras, acaba dejándote en la mano, y casi siempre en momentos en que no se puede retrasar el compromiso al que estaba en camino. Ahora, imagínese que su coche fuera “inteligente” suficiente para percibir cuando alguno de sus componentes está cerca de romperse. Y si él pudiera avisarte para visitar el mecánico, y aún indicarle qué pieza necesita reparación?
En la fábrica, situaciones parecidas ocurren, las máquinas se rompe al final del mes, retrasando la producción cuando la línea ya está sobrecargada, corriendo detrás de la meta. Y peor, el tiempo que se dedica a la investigación y la solución del problema hace que otras máquinas que dependen de la que se rompió también paren. Y en este caso, si la máquina era “inteligente” suficiente para percibir que está cerca de romperse, y podría avisar al responsable del mantenimiento que necesita servicio en la pieza X?
Estas “inteligencias” citadas en ambos ejemplos son lo que llamamos Mantenimiento Predictivo.
La comprensión de los tipos de mantenimiento
Hay tres tipos de mantenimiento, son:
- Mantenimiento Correctivo: Cuando el equipo tiene algún pane, y necesita reparaciones para volver a funcionar. Normalmente toma mucho tiempo, pues el equipo queda inutilizable mientras los expertos investigan la causa del problema. Además, por ser inesperado, puede causar muchos problemas en la cadena de producción
- Mantenimiento Preventivo: Se realiza utilizando algún parámetro externo la máquina para determinar cuándo debe ocurrir. Por ejemplo, se realiza cada 480 horas de equipo operando, o cada 10000 km rodados por el automóvil. No necesariamente garantizan que el equipo no falla, pero reducen mucho esa posibilidad. Como el intervalo entre mantenimientos está predeterminado, es posible que no reflejen todo el contexto en el que se inserta el equipo. Por consiguiente, puede llevar a gastos con mantenimiento innecesario, desperdicio de partes que todavía estaban buenas para operar, etc.
- Mantenimiento Predictivo: El equipo se monitorea, sabiendo en todo momento el estado de sus componentes. Con esto también prevé cuando hay un fallo inminente, avisando que necesita mantenimiento y dando informaciones que ayudan al técnico a saber qué parte del equipo necesita de mantenimiento. Con el uso del Mantenimiento Predictivo se reduce el riesgo de falla y también el desperdicio de tiempo y material con mantenimiento preventivo.
¿Cómo se puede aplicar Mantenimiento Predictivo?
Como se explicó en el post IoT and predictive maintenance, do Bosch ConnectedWorld Blog, el Mantenimiento Predictivo se viabiliza a partir de tres pasos:
- Captura de datos de sensores: Colocar varios sensores en el recurso a ser monitoreado. Diversas magnitudes en el equipo deben ser medidas con frecuencia, y disponibles para procesamiento. Debido al gran volumen de datos adquiridos, estos datos pueden ser considerados Big Data. En la mayor parte del tiempo, la medición seguirá un patrón, pero una desviación de este patrón puede indicar un evento.
- Facilitar la comunicación de datos: Los datos recopilados en el recurso deben transferirse a una central de procesamiento de datos. Para un buen tiempo de respuesta a cambios en el patrón de medición de los sensores, es ideal que la transferencia de los datos a la central no se demore.
- Hacer predicciones (IA): Los datos de los sensores se evalúan constantemente, y se comparan con los patrones históricos. Cuando un patrón similar a aquel que suele suceder antes de un evento (una ruptura, por ejemplo), el sistema reporta el comportamiento. Con ello, acciones deben ser tomadas por el sistema para revertir el evento, como por ejemplo, avisar al responsable del mantenimiento que la función X tiende a presentar el defecto Y en la pieza Z en las próximas horas.
¿Cómo entender tantos datos?
Ninguno de los tres pasos descritos es tarea fácil, pero el más desafiante es el tercero: hacer predicciones.
Para ello, se inicia por la selección y preprocesamiento de los datos a ser procesados (Data Mining). En el algoritmo de Data Mining, los expertos en el recurso y los científicos de datos pueden representar explícitamente conocimientos adquiridos por la experiencia. El algoritmo ampliará este conocimiento, encontrando relaciones entre las variables disponibles.
Después del preprocesamiento, viene la parte de análisis de comportamiento y patrones. Esta parte se hace con algoritmos de Inteligencia Artificial, que son capaces de aprender cómo son los patrones que generan cada evento. Se utilizan para monitorear y detectar estos eventos.
Detectado el evento, el programa verifica si es necesaria una acción, y se inicia. Esta acción puede ser desde un control en la máquina hasta el envío de mensajes al personal responsable.
¿Cómo empezar?
Implementar el Mantenimiento Predictivo en una fábrica entera ciertamente no es tarea fácil (o barata), pero hemos visto que los beneficios son muchos. Un proyecto ambicioso de este tamaño requiere pequeños pasos para su implementación con éxito.Sugerimos que empiece evaluando qué herramientas usadas en el Mantenimiento Predictivo su fábrica ya posee y listan los equipos con mayor nivel de conectividad y mayor cantidad de sensores disponibles.
¿Usted ya centraliza los datos recopilados por estos equipos? Compruebe también si el fabricante recoge, almacena y proporciona datos sobre sus equipos. Estos datos se pueden utilizar para la comparación y el entrenamiento de un algoritmo de Inteligencia Artificial.
Y su fábrica, posee sistemas que pueden ser utilizados / adaptados para implantación del Mantenimiento Predictivo? Cuéntanos en los comentarios.
Recuerde que podemos ayudarle en estos proyectos a su fábrica, basta con ponerse en contacto con nosotros.[:]